7 Human Errors That Shorten the Lifespan of Industrial Rubber Linings
Since its founding year in 1981, end-users have relied on the Blair Rubber Co. to help find solutions to the premature failure of their primary containment systems.
Blair Rubber Co. has devoted countless man-hours to the research and development of innovative rubber linings and adhesive systems – from natural rubber and Neoprene® to Chlorobutyl, Bromobutyl, Nitrile and even our highly-resilient EPDM linings.
Customers are in good hands with Blair Rubber because we’re the only U.S.-based manufacturer with a complete line of corrosion-resistant rubber linings and conveyor belt splice products. We have what they need.
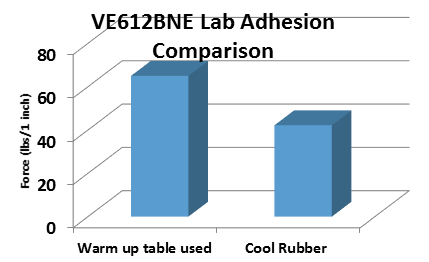
Human error can stop production in its tracks. Errors of one sort or another can lead to rubber lining failures within storage tanks and process vessels. We’ve outlined some of the common causes below.
From lack of effort or attention during installation to the wrong environmental conditions or product selection, these mistakes can reduce the lifetime of rubber panels covering substrates and sabotage primary containment.
When Applying Rubber Panels:
- Missed spots while rolling and stitching, due to merely laying down rubber panels without “elbow grease”
- Short skives causing seams to lift
- Applying rubber to cold metal, <50°F
- Poor management of temperature/humidity when applying primers & adhesives before applying the panels
- Dropping tools
When Handling Rubber Panels:
- Gouges from work boots, ladders or scaffolds
- Keeping a clean work area
- Applying force to chemical cure flange linings -over tightening
When Selecting Types of Rubber Per Application:
- Matching the incorrect rubber lining to the chemical service
- Using inappropriate adhesive systems for tie gum layer
- Use of unapproved solvents, organic materials to fight foam or solidification
The proper specification and application of our rubber linings for primary containment is the key to success both for ourselves and for those with whom we do business.
Since the common denominator in most issues of premature lining failure is the human factor, we wanted to highlight some of the ways that better preparation and mindful application/installation of our rubber products can lead to increased product longevity and performance.
Below are seven errors that can be prevented with the right amount of education and procedural diligence.
One – Lack of Attention and “Elbow Grease” while Rolling and Stitching the Rubber Panels
While there are many factors that can influence the quality of workmanship during the installation of internal tank linings, the bottom line is that installers need to be thorough and rigorous during installation. Much like wallpaper applications on the walls of a home, panels must be applied so that there is intimate contact between the panels and the substrate at all points to avoid air pockets and bubbles. Squeegeeing alone normally does not accomplish this.
Two – Short Skives that Cause Rubber Panel Seams to Lift Over Time
The interconnection of rubber panels must be managed wisely, with great attention to craftsmanship in the installation process.
“The skive is the edge of the rubber panel,” explains Gregg Reinmann, Manager of Technical and Quality Assurance at Blair Rubber. “Putting a bevel or an angle on the skives during application is essential. When it’s at 90 degrees or at a very sharp edge, you will tend to have problems over time between the panels. Properly skiving the panels at a 30-degree to 45-degree angle where the rubber makes a transition from two layers-thick down to one layer thick works better.”
Three – Mismanagement of Temperature and Humidity during the Application Process
With chemical processes at-work between the lining adhesive and the lining itself, as well as the inherent differences between the substrate and the rubber lining, temperature and humidity can complicate matters severely. Professional installation must take into account both these environmental factors.
A general requirement for rubber-panel installations is that there must be a difference between the dew point and the substrate of more than 5 degrees Fahrenheit. If the humidity is too high, it will draw moisture onto the metal substrate and that water will be trapped when the rubber is placed on its surface. When the rubber is then cured via steam, that trapped water will turn to vapor and push the rubber off the wall and make blisters.
The temperature also needs to be greater than 50 degrees F for installing the panels. As Reinmann explains it, “When it’s less than that temperature, the metal just robs the rubber of its heat and thus its flexibility. When you heat the rubber up and then apply the adhesive, the rubber is very receptive to the adhesive and wants to bond to it. If it’s cold, it just doesn’t bond as well and you’ll have problems with more trapped air, or conform the rubber to the shape of the substrate, etc. Within industrial settings, you’re not just laying down the panels on completely flat surfaces….you’ve got agitators, baffles and what not and when it’s cold, the rubber wants to stay flat and not conform to the shape of the surface it’s being applied to. There won’t be a strong bond between the rubber and the substrate in that case.”
Four – Damage to the Rubber Panels via Tools and Equipment
Although this may seem like a “no-brainer,” it’s a common problem during the installation process that the rubber panels become damaged with gouges due to dropped hand tools, ladder marks, scaffolding…even work boots, which may be carrying small bits of rock or other sharp debris that can penetrate the panels. While rubber is remarkably durable, it is susceptible to incisions made by sharp objects, and so to preserve its impermeability the panels must be treated very gently as they are applied.
Five – Failure to Keep a Clean Work Area
Similar to number Four, this is an easy step for proactive panel installations if it is remembered. Failure to keep a clean work space means that debris can come into contact with the rubber panels, or become lodged in work shoes and thus gouge the panels for damage down the road. “Many companies insist that workers remove their shoes before they enter the tanks to inspect or clean them,” Reinmann reveals.
Six – Applying Force to or Over-Tightening Chemical-Cure Flange Linings
The most frequent error and the highest risk when it comes to handling our rubber linings is applying too much torque to the chemical-cured flange linings. Over tightening. A popular illustration involves the example of changing an automotive tire – a star pattern is used when tightening the lug nuts so that too much force to one side of the wheel does not occur; otherwise a cockeyed mating of the wheel on the hub can happen. “We see people do this in the field all the time with our linings,” Reinmann admits. “Or they’ll use just too much force and they just squeeze the rubber out of the flange completely. They think that tighter is better, but that’s not necessarily true.”
Seven – Inappropriately Matching Rubber Types and Adhesives to Substrates or Application Usage
With nine different categories of linings and many sub-categories within those main selections, as well as several different primers, sealants and adhesives available from Blair, there are a vast number of potential product combinations for primary containment needs – not all appropriate for every circumstance or scenario. Product understanding for maximum performance is essential!
As Reinmann concludes, “There are probably 4 or 5 different kinds of materials you could use for a particular situation or application setting. There’s probably a best one for the specific need, and there are certainly some poor choices. Education matters.”
Has this article caused you to think a bit more deeply about your company’s rubber linings needs? Or perhaps you’re new to the industry and looking for primary containment options for the first time? Either way, Blair Rubber wants to answer your questions and business needs. Please contact us for a no-obligation conversation about our many rubber products and how they can enhance your industrial process.
Take a look at our exhaustive and very helpful Tank Lining Inspection and Maintenance Strategy – free from Blair Rubber!